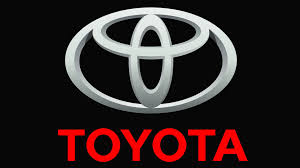
Even though the concept of just-in-time manufacturing was pioneered by the Japanese car maker Toyota, its decision to stockpile chips used in the car industry and which is now facing a shortage globally seems to be apt. The car maker has been stocking up this key component of cars for a decade starting with the Fukushima disaster.
Toyota had realised that the lead-time for semiconductors was far too long for the company to tackle any lead-time for semiconductors soon after the Fukushima disaster March 11, 2011 broke down the supply chains of the largest automaker of the world by manufacturing volume.
Based on that experience, a business continuity plan (BCP) was launched by Toyota under which it directed its suppliers to keep build in stocks for that could worth supplies of between two to six months’ of chips that can be used by the car maker. The stockpiling of the chips should depend on the time that is required from ordering to delivery of the chips according to reports.
This has helped the car maker from being largely insulated from the global shortage of semiconductors after a surge in demand for chips for electrical goods during the Covid-19 pandemic as people were forced to stay back home because of lockdowns and other restrictions. The shortage of chips for cars has forced many auto companies to suspend or reduce production to match supply of chips.
“Toyota was, as far as we can tell, the only automaker properly equipped to deal with chip shortages,” said a source familiar with Harman International, which specialises in car audio systems, displays and driver assistance technology to the news agency Reuters.
The market was surprised when Toyota announced last month that its production will not be affected to any significant degree because of the chip shortages even while rival companies like Volkswagen, General Motors, Ford, Honda and Stellantis and others reported closure or suspension of a part of their production because of the chip shortage.
Toyota however has instead increased its target for vehicle production for the current fiscal year ending this month while also enhancing its earnings forecast by 54 per cent for the full year.
Since the 2011 earthquake, the way it purchases microcontroller units (MCUs) and microcontroller units (MCUs) has been changed by Toyota. The earthquake had resulted in a tsunami and a meltdown at the nuclear power plant at Fukushima.
Following the earthquake and the disaster, an estimation that purchasing of more than 1,200 parts and materials for Toyota would be affected, the company estimated, and therefore created a list of 500 priority items that would need supply security in the future. That list included semiconductors made by key Japanese chip supplier Renesas Electronics.
One of the targets of implementing the lean inventories strategy at Toyota was to become reactive to inefficiencies and risks in the supply chain, identification of the bottlenecks that could potentially be the most damaging and to find out ways to tackle the problem, according to a Toyota spokesman.
“The BCP for us was a classic lean solution,” he said.
(Source:www.reuters.com)
Toyota had realised that the lead-time for semiconductors was far too long for the company to tackle any lead-time for semiconductors soon after the Fukushima disaster March 11, 2011 broke down the supply chains of the largest automaker of the world by manufacturing volume.
Based on that experience, a business continuity plan (BCP) was launched by Toyota under which it directed its suppliers to keep build in stocks for that could worth supplies of between two to six months’ of chips that can be used by the car maker. The stockpiling of the chips should depend on the time that is required from ordering to delivery of the chips according to reports.
This has helped the car maker from being largely insulated from the global shortage of semiconductors after a surge in demand for chips for electrical goods during the Covid-19 pandemic as people were forced to stay back home because of lockdowns and other restrictions. The shortage of chips for cars has forced many auto companies to suspend or reduce production to match supply of chips.
“Toyota was, as far as we can tell, the only automaker properly equipped to deal with chip shortages,” said a source familiar with Harman International, which specialises in car audio systems, displays and driver assistance technology to the news agency Reuters.
The market was surprised when Toyota announced last month that its production will not be affected to any significant degree because of the chip shortages even while rival companies like Volkswagen, General Motors, Ford, Honda and Stellantis and others reported closure or suspension of a part of their production because of the chip shortage.
Toyota however has instead increased its target for vehicle production for the current fiscal year ending this month while also enhancing its earnings forecast by 54 per cent for the full year.
Since the 2011 earthquake, the way it purchases microcontroller units (MCUs) and microcontroller units (MCUs) has been changed by Toyota. The earthquake had resulted in a tsunami and a meltdown at the nuclear power plant at Fukushima.
Following the earthquake and the disaster, an estimation that purchasing of more than 1,200 parts and materials for Toyota would be affected, the company estimated, and therefore created a list of 500 priority items that would need supply security in the future. That list included semiconductors made by key Japanese chip supplier Renesas Electronics.
One of the targets of implementing the lean inventories strategy at Toyota was to become reactive to inefficiencies and risks in the supply chain, identification of the bottlenecks that could potentially be the most damaging and to find out ways to tackle the problem, according to a Toyota spokesman.
“The BCP for us was a classic lean solution,” he said.
(Source:www.reuters.com)