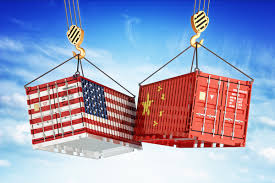
The latest round of tariffs imposed by the U.S. on Chinese imports is proving to be far more disruptive than the trade war that unfolded in 2018. Back then, many businesses managed to adjust by negotiating prices, finding alternative suppliers, or absorbing some of the costs. This time, however, those options are dwindling. Supply chains have already been stretched thin by years of trade tensions, the COVID-19 pandemic, and global inflationary pressures. With limited flexibility left, companies on both sides of the Pacific are feeling the strain more acutely than ever before.
For manufacturers, the situation is particularly grim. Production schedules are being upended as orders shrink and costs climb. Many businesses that managed to weather the previous trade war are now finding themselves out of options. The ability to move production elsewhere or pass costs on to customers is no longer a viable strategy for many, leaving them with difficult choices about their future.
Chinese Factories Face a Breaking Point
Low-end Chinese manufacturers are among the hardest hit. Many of these businesses already operate on razor-thin profit margins, and the additional tariffs are pushing them dangerously close to collapse. Unlike in 2018, when some companies were able to absorb price hikes or negotiate discounts with their U.S. clients, there is simply no more room to maneuver.
Factories that produce lower-cost goods, such as Christmas decorations, toys, and household items, are particularly vulnerable. These businesses often lack the financial cushion to withstand major disruptions. With fewer orders and no ability to reduce prices further, many Chinese manufacturers are being forced to take significant losses just to keep operations running.
Adding to the challenges faced by Chinese manufacturers are rising production costs. Since the last trade war, wages have continued to climb, and raw materials have become more expensive. These increases were already pressuring suppliers before the new tariffs were introduced, making it nearly impossible for businesses to offer price reductions to their U.S. clients.
Higher costs for materials such as aluminum, plastics, and textiles are also eating into profits. While some manufacturers might have absorbed tariff-related costs in 2018, the current situation leaves little room for such adjustments. With no viable way to cut expenses, the burden of the tariffs is hitting suppliers hard, forcing them to make difficult decisions about pricing and production levels.
U.S. Retailers Struggle to Negotiate Relief
American retailers are feeling the squeeze as well. Major companies like Walmart and Costco rely heavily on Chinese suppliers, but their ability to negotiate better prices has been severely weakened. While many retailers have pushed for across-the-board price cuts from their suppliers, the response has been limited.
Most Chinese manufacturers are unable to meet the demands for a 10% reduction in prices, with the best they can offer being discounts of 3% to 7%. This leaves U.S. retailers with a difficult choice: absorb the extra costs themselves, pass them on to consumers, or look for new suppliers—an option that is not always feasible due to concerns about quality and reliability.
One significant change in supplier behavior since the 2018 trade war is the shift in payment terms. After many Chinese manufacturers suffered financial losses when U.S. buyers refused to pay higher costs on tariffed goods, suppliers are now demanding upfront payments.
This new approach is designed to mitigate risks, but it also puts additional strain on American importers. Businesses that were accustomed to paying 30 to 90 days after receiving goods are now required to pay in advance, which ties up cash flow and limits their financial flexibility. For small and mid-sized companies, this change can be particularly burdensome.
Some American businesses are looking beyond China for manufacturing solutions. Vietnam and other Southeast Asian countries have been viewed as potential alternatives, but the transition is far from seamless.
One major issue is cost. While Vietnam may offer lower labor costs in some industries, overall production expenses—including infrastructure, logistics, and raw materials—can still be high. Additionally, Chinese manufacturers have decades of experience and efficiency, which is difficult to replicate elsewhere. Businesses moving production out of China face delays, quality control issues, and logistical headaches that make relocation a less attractive option than it initially appears.
Mass Layoffs Threaten China’s Workforce
With Chinese manufacturers struggling to keep operations afloat, the risk of widespread layoffs is growing. In the previous trade war, millions of manufacturing jobs were lost, and the current situation suggests a similar or even worse outcome.
Factories that once employed thousands of workers are now operating at reduced capacity or shutting down altogether. As demand shrinks, businesses have little choice but to cut labor costs. This not only affects factory workers but also has a ripple effect on the broader economy, leading to weaker consumer spending and economic instability.
Unlike in 2018, when Chinese provincial governments stepped in with subsidies to support struggling businesses, the current economic climate makes such assistance unlikely. Many local governments are burdened with debt, in large part due to a prolonged real estate crisis and declining revenues.
With limited financial resources, regional authorities are unable to provide the same level of relief that helped factories stay afloat in the past. This leaves manufacturers with fewer options for financial assistance, increasing the likelihood of factory closures and job losses.
U.S. Businesses Face Unintended Consequences
One of the primary goals of the tariffs was to bring manufacturing jobs back to the United States. However, instead of reshoring production, the tariffs are driving up costs for American companies and consumers.
The higher costs of imported goods are squeezing profit margins, making it harder for U.S. businesses to compete. For some, moving production back to the U.S. is simply not feasible due to labor costs and infrastructure limitations. Instead of benefiting American workers, the tariffs are making it more expensive for businesses to operate, with few clear benefits in return.
China’s Domestic Market Offers Little Relief
Some policymakers have suggested that Chinese manufacturers could shift their focus to domestic consumers. However, this is easier said than done. China is already dealing with issues of overcapacity, meaning that factories are producing more goods than the local market can absorb.
Furthermore, weak consumer demand in China makes this strategy impractical. The country’s slowing economic growth and cautious consumer spending habits limit the ability of businesses to replace lost U.S. orders with local sales. Without a strong domestic market to fall back on, Chinese manufacturers remain heavily reliant on exports, leaving them vulnerable to the trade war’s ongoing disruptions.
One of the most difficult aspects of the current trade war is the lack of clear direction. Both U.S. and Chinese businesses are struggling to plan for the future because trade policies remain unpredictable.
Companies need stability to make long-term decisions about investment, production, and hiring. However, with tariffs being imposed and adjusted with little warning, businesses are left in a constant state of uncertainty. This unpredictability makes it difficult for both American and Chinese companies to develop effective strategies for navigating the ongoing trade conflict.
Consumers to Bear the Ultimate Cost
Ultimately, the biggest losers in the trade war may be American consumers. As businesses face higher costs, many have no choice but to pass them on to customers. Prices for goods ranging from electronics to household essentials are already rising, and further increases are expected as tariffs continue to take effect.
For the average consumer, this means higher prices at the checkout counter with little relief in sight. The intention behind the tariffs may have been to strengthen American industry, but the reality is that they are creating additional financial burdens for businesses and households alike.
(Source:www.reuters.com)
For manufacturers, the situation is particularly grim. Production schedules are being upended as orders shrink and costs climb. Many businesses that managed to weather the previous trade war are now finding themselves out of options. The ability to move production elsewhere or pass costs on to customers is no longer a viable strategy for many, leaving them with difficult choices about their future.
Chinese Factories Face a Breaking Point
Low-end Chinese manufacturers are among the hardest hit. Many of these businesses already operate on razor-thin profit margins, and the additional tariffs are pushing them dangerously close to collapse. Unlike in 2018, when some companies were able to absorb price hikes or negotiate discounts with their U.S. clients, there is simply no more room to maneuver.
Factories that produce lower-cost goods, such as Christmas decorations, toys, and household items, are particularly vulnerable. These businesses often lack the financial cushion to withstand major disruptions. With fewer orders and no ability to reduce prices further, many Chinese manufacturers are being forced to take significant losses just to keep operations running.
Adding to the challenges faced by Chinese manufacturers are rising production costs. Since the last trade war, wages have continued to climb, and raw materials have become more expensive. These increases were already pressuring suppliers before the new tariffs were introduced, making it nearly impossible for businesses to offer price reductions to their U.S. clients.
Higher costs for materials such as aluminum, plastics, and textiles are also eating into profits. While some manufacturers might have absorbed tariff-related costs in 2018, the current situation leaves little room for such adjustments. With no viable way to cut expenses, the burden of the tariffs is hitting suppliers hard, forcing them to make difficult decisions about pricing and production levels.
U.S. Retailers Struggle to Negotiate Relief
American retailers are feeling the squeeze as well. Major companies like Walmart and Costco rely heavily on Chinese suppliers, but their ability to negotiate better prices has been severely weakened. While many retailers have pushed for across-the-board price cuts from their suppliers, the response has been limited.
Most Chinese manufacturers are unable to meet the demands for a 10% reduction in prices, with the best they can offer being discounts of 3% to 7%. This leaves U.S. retailers with a difficult choice: absorb the extra costs themselves, pass them on to consumers, or look for new suppliers—an option that is not always feasible due to concerns about quality and reliability.
One significant change in supplier behavior since the 2018 trade war is the shift in payment terms. After many Chinese manufacturers suffered financial losses when U.S. buyers refused to pay higher costs on tariffed goods, suppliers are now demanding upfront payments.
This new approach is designed to mitigate risks, but it also puts additional strain on American importers. Businesses that were accustomed to paying 30 to 90 days after receiving goods are now required to pay in advance, which ties up cash flow and limits their financial flexibility. For small and mid-sized companies, this change can be particularly burdensome.
Some American businesses are looking beyond China for manufacturing solutions. Vietnam and other Southeast Asian countries have been viewed as potential alternatives, but the transition is far from seamless.
One major issue is cost. While Vietnam may offer lower labor costs in some industries, overall production expenses—including infrastructure, logistics, and raw materials—can still be high. Additionally, Chinese manufacturers have decades of experience and efficiency, which is difficult to replicate elsewhere. Businesses moving production out of China face delays, quality control issues, and logistical headaches that make relocation a less attractive option than it initially appears.
Mass Layoffs Threaten China’s Workforce
With Chinese manufacturers struggling to keep operations afloat, the risk of widespread layoffs is growing. In the previous trade war, millions of manufacturing jobs were lost, and the current situation suggests a similar or even worse outcome.
Factories that once employed thousands of workers are now operating at reduced capacity or shutting down altogether. As demand shrinks, businesses have little choice but to cut labor costs. This not only affects factory workers but also has a ripple effect on the broader economy, leading to weaker consumer spending and economic instability.
Unlike in 2018, when Chinese provincial governments stepped in with subsidies to support struggling businesses, the current economic climate makes such assistance unlikely. Many local governments are burdened with debt, in large part due to a prolonged real estate crisis and declining revenues.
With limited financial resources, regional authorities are unable to provide the same level of relief that helped factories stay afloat in the past. This leaves manufacturers with fewer options for financial assistance, increasing the likelihood of factory closures and job losses.
U.S. Businesses Face Unintended Consequences
One of the primary goals of the tariffs was to bring manufacturing jobs back to the United States. However, instead of reshoring production, the tariffs are driving up costs for American companies and consumers.
The higher costs of imported goods are squeezing profit margins, making it harder for U.S. businesses to compete. For some, moving production back to the U.S. is simply not feasible due to labor costs and infrastructure limitations. Instead of benefiting American workers, the tariffs are making it more expensive for businesses to operate, with few clear benefits in return.
China’s Domestic Market Offers Little Relief
Some policymakers have suggested that Chinese manufacturers could shift their focus to domestic consumers. However, this is easier said than done. China is already dealing with issues of overcapacity, meaning that factories are producing more goods than the local market can absorb.
Furthermore, weak consumer demand in China makes this strategy impractical. The country’s slowing economic growth and cautious consumer spending habits limit the ability of businesses to replace lost U.S. orders with local sales. Without a strong domestic market to fall back on, Chinese manufacturers remain heavily reliant on exports, leaving them vulnerable to the trade war’s ongoing disruptions.
One of the most difficult aspects of the current trade war is the lack of clear direction. Both U.S. and Chinese businesses are struggling to plan for the future because trade policies remain unpredictable.
Companies need stability to make long-term decisions about investment, production, and hiring. However, with tariffs being imposed and adjusted with little warning, businesses are left in a constant state of uncertainty. This unpredictability makes it difficult for both American and Chinese companies to develop effective strategies for navigating the ongoing trade conflict.
Consumers to Bear the Ultimate Cost
Ultimately, the biggest losers in the trade war may be American consumers. As businesses face higher costs, many have no choice but to pass them on to customers. Prices for goods ranging from electronics to household essentials are already rising, and further increases are expected as tariffs continue to take effect.
For the average consumer, this means higher prices at the checkout counter with little relief in sight. The intention behind the tariffs may have been to strengthen American industry, but the reality is that they are creating additional financial burdens for businesses and households alike.
(Source:www.reuters.com)