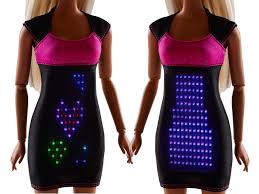
While wearables are gaining popularity both among select range of customers and present innumerable opportunities for fashion designers, the supply chain isn’t up to speed.
This is the outlook of a panel of wearable technology and fashion experts about the recent trends of wearabls.
“The biggest pet peeve I’ve experienced is there are two very, very diverse supply chains: the fashion supply chain and the manufacture of electronics, and nowhere do they merge,” Fashion Institute of Technology (FIT) Professor Michael Reidbord said at the IDTechEx Wearable USA.
“You have to engage the creative element way, way early in the supply chain,” Reidbord said.
Most wearables haven’t been very fashionable until products such as the Apple Watch and Motorola Moto 360 smartwatch emerged. Industry experts claim that there are several hurdles to cross before technically complex garments will hang in closets even as organizations such as London’s Fashion Innovation Agency aim to bridge the gap between designers and technologists.
“When you think of the transition from fabric to the garment, you have skill sets that don’t exist in contract manufacturing that will be needed. Electrical engineers see making clothing as simple, but it’s quite complicated,” said Clare King, president of Propel LLC, a company that develops textile related technologies for the U.S. military and firefighters.
The issues related to the textiles, conductive threads, and ways of connecting them to electronic equipment have prevented the development of commercially successful electronic fabrics. King said that the wearables market is several years from realizing a successful manufacturing and commercial market.
Industrial processes or regular washing is still not possible with the existing e-textiles s they lack the strength to withstand the processes. Silver conductive threads are particularly susceptible to shredding.
E-textiles seem to only be in use in fitness or compression-type clothing eve as conductive threads have largely been used in the DIY space. While several experiments are being done with copper and stainless steel but commercialization of these are still years away, according to the FIT professor.
“The current platform of conductive yarns and fibers cause some production problems...it hasn’t been commercialized, probably, because this technology is part of Department of Defense-funded companies,” King said.
“If companies can make a viable yarn out of one of the conductive polymers that have been developed, that will be a game changer,” king added.
Despite the limitation of the use of conductive wires for wearable clothes, advances in semiconductor technology can provide a solution and would profoundly affect wearable fashion. For example, Intel’s button Curie module and partnership with luxury glasses brand house Luxottica goes well for the future of fashionable wearables.
“There’s a high degree of integration now that you have a very, very small chip so you can get Wi-Fi, Bluetooth, and even cellular connectivity on a single chip,” said Marc Naddell, vice president of ecosystems at MediaTek.
“With that level of integration, you have a reduced cost and size, which are all very important for any wearable product,” he added.
(Source:www.eetimes.com)
This is the outlook of a panel of wearable technology and fashion experts about the recent trends of wearabls.
“The biggest pet peeve I’ve experienced is there are two very, very diverse supply chains: the fashion supply chain and the manufacture of electronics, and nowhere do they merge,” Fashion Institute of Technology (FIT) Professor Michael Reidbord said at the IDTechEx Wearable USA.
“You have to engage the creative element way, way early in the supply chain,” Reidbord said.
Most wearables haven’t been very fashionable until products such as the Apple Watch and Motorola Moto 360 smartwatch emerged. Industry experts claim that there are several hurdles to cross before technically complex garments will hang in closets even as organizations such as London’s Fashion Innovation Agency aim to bridge the gap between designers and technologists.
“When you think of the transition from fabric to the garment, you have skill sets that don’t exist in contract manufacturing that will be needed. Electrical engineers see making clothing as simple, but it’s quite complicated,” said Clare King, president of Propel LLC, a company that develops textile related technologies for the U.S. military and firefighters.
The issues related to the textiles, conductive threads, and ways of connecting them to electronic equipment have prevented the development of commercially successful electronic fabrics. King said that the wearables market is several years from realizing a successful manufacturing and commercial market.
Industrial processes or regular washing is still not possible with the existing e-textiles s they lack the strength to withstand the processes. Silver conductive threads are particularly susceptible to shredding.
E-textiles seem to only be in use in fitness or compression-type clothing eve as conductive threads have largely been used in the DIY space. While several experiments are being done with copper and stainless steel but commercialization of these are still years away, according to the FIT professor.
“The current platform of conductive yarns and fibers cause some production problems...it hasn’t been commercialized, probably, because this technology is part of Department of Defense-funded companies,” King said.
“If companies can make a viable yarn out of one of the conductive polymers that have been developed, that will be a game changer,” king added.
Despite the limitation of the use of conductive wires for wearable clothes, advances in semiconductor technology can provide a solution and would profoundly affect wearable fashion. For example, Intel’s button Curie module and partnership with luxury glasses brand house Luxottica goes well for the future of fashionable wearables.
“There’s a high degree of integration now that you have a very, very small chip so you can get Wi-Fi, Bluetooth, and even cellular connectivity on a single chip,” said Marc Naddell, vice president of ecosystems at MediaTek.
“With that level of integration, you have a reduced cost and size, which are all very important for any wearable product,” he added.
(Source:www.eetimes.com)